See This Report on Alcast Company
See This Report on Alcast Company
Blog Article
An Unbiased View of Alcast Company
Table of ContentsAlcast Company - Questions7 Easy Facts About Alcast Company ExplainedFascination About Alcast CompanyThe Main Principles Of Alcast Company Alcast Company - An OverviewOur Alcast Company Ideas
Chemical Contrast of Cast Aluminum Alloys Silicon advertises castability by lowering the alloy's melting temperature and boosting fluidity during spreading. In addition, silicon contributes to the alloy's stamina and put on resistance, making it important in applications where resilience is important, such as automobile parts and engine parts.It likewise boosts the machinability of the alloy, making it less complicated to refine right into ended up items. In this means, iron adds to the overall workability of aluminum alloys. Copper enhances electrical conductivity, making it advantageous in electric applications. It also improves corrosion resistance and contributes to the alloy's overall strength.
Manganese contributes to the toughness of light weight aluminum alloys and boosts workability. Magnesium is a light-weight aspect that offers stamina and impact resistance to aluminum alloys.
Unknown Facts About Alcast Company
Zinc boosts the castability of aluminum alloys and aids manage the solidification procedure throughout spreading. It enhances the alloy's strength and firmness.
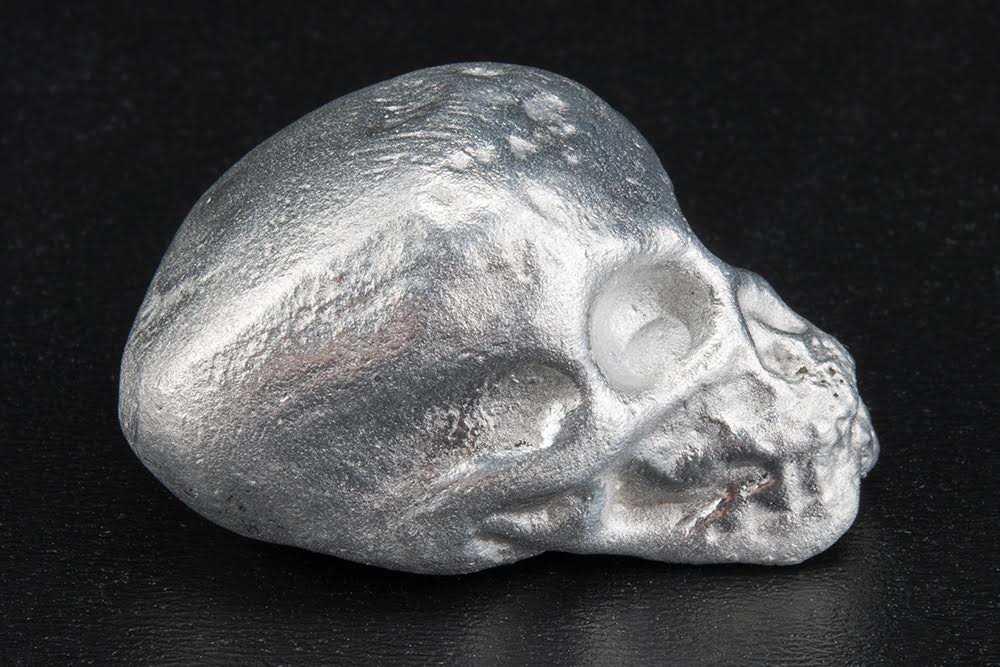
The key thermal conductivity, tensile strength, return stamina, and prolongation vary. Select suitable raw materials according to the efficiency of the target item created. Among the above alloys, A356 has the greatest thermal conductivity, and A380 and ADC12 have the most affordable. The tensile restriction is the contrary. A360 has the ideal yield strength and the greatest elongation price.
The Best Strategy To Use For Alcast Company
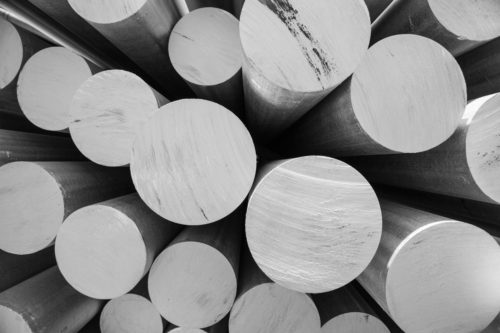
Its unique buildings make A360 a beneficial choice for accuracy spreading in these markets, enhancing item durability and quality. aluminum metal casting. Light weight aluminum alloy 380, or A380, is a widely utilized casting alloy with several distinctive qualities.
In accuracy casting, light weight aluminum 413 radiates in the Consumer Electronics and Power Equipment markets. It's typically made use of to craft intricate components like smart device real estates, video camera bodies, and power tool coverings. Its precision is amazing, with tight tolerances approximately 0.01 mm, making certain flawless item setting up. This alloy's premium corrosion resistance makes it an outstanding choice for exterior applications, ensuring long-lasting, durable items in the stated industries.
An Unbiased View of Alcast Company
Once you have actually made a decision that the aluminum pass away casting procedure is appropriate for your job, an important next action is picking one of the most proper alloy. The aluminum alloy you choose will considerably influence both the casting process and the homes of the final item. Due to this, you need to make your decision carefully and take an enlightened technique.
Establishing the most ideal aluminum alloy for your application will imply weighing a broad range of attributes. The very first group addresses alloy features that influence the production procedure.
The 4-Minute Rule for Alcast Company
The alloy you select for die casting straight affects several facets of the spreading process, like how simple the alloy is to collaborate with and if it is vulnerable to casting flaws. Warm breaking, likewise referred to as solidification splitting, is a common die casting defect for light weight aluminum alloys that can lead to interior or surface-level tears or splits.
Specific light weight aluminum alloys are a lot more at risk to warm splitting than others, and your choice ought to consider this. blog Another usual flaw found in the die spreading of light weight aluminum is die soldering, which is when the cast stays with the die walls and makes ejection tough. It can damage both the actors and the die, so you need to search for alloys with high anti-soldering buildings.
Deterioration resistance, which is already a significant feature of light weight aluminum, can differ substantially from alloy to alloy and is a necessary characteristic to take into consideration depending upon the ecological problems your product will be subjected to (Foundry). Use resistance is one more residential or commercial property frequently sought in light weight aluminum items and can differentiate some alloys
Report this page